Installations in marine and offshore environments
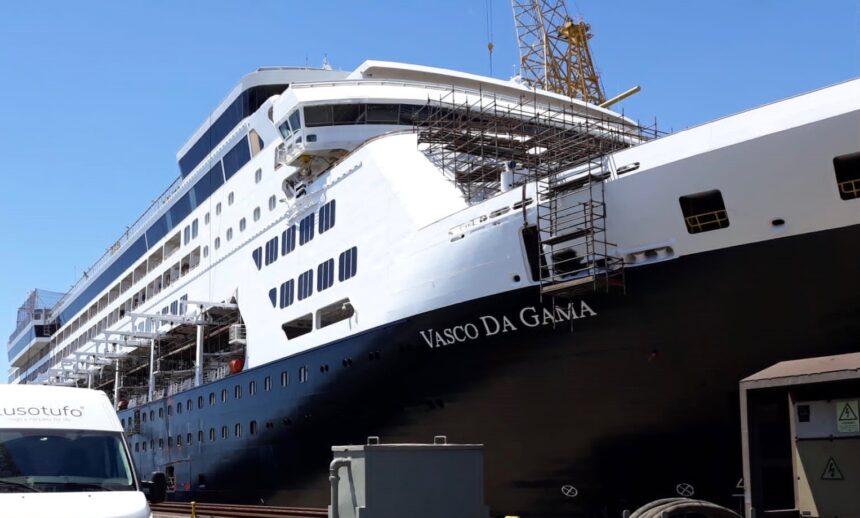
John Green, one of F. Ball’s technical service officers, advises on ensuring compliance while achieving a high-performance, aesthetically pleasing flooring finish.
Amongst other special considerations when installing floorcoverings in marine environments, contractors must ensure that smoothing compounds and adhesives meet appropriate fire safety standards for ships at sea, including low flame spread standards and low smoke toxicity.
Until recently, contractors could look for the IMO ‘wheel mark’ logo on product packaging to check compliance with International Maritime Organization (IMO) standards as well as the EU Marine Equipment Directive (MED).
As well as the requirement for a product to carry the IMO wheel mark, specialist features are often required for marine and offshore environments.
Subfloor preparation
Just as when installing floorcoverings on land, contractors should make sure the subfloor is structurally sound, dry and free of any contaminants or debris. The application of a smoothing compound is recommended to create a perfectly smooth surface for floorcoverings.
A common subfloor type in crew and passenger areas on board ships is steel decking, which is liable to ‘flex’ slightly as a result of the motion of a vessel, as well foot traffic and temperature fluctuations, so any smoothing compound selected for use over this type of subfloor needs be able to cope with these movements. F. Ball’s Stopgap 700 was developed especially for this purpose. The smoothing compound is fibre-reinforced, allowing it to accommodate minor subfloor movement while providing a strong, stable base for the receipt of floorcoverings.
F. Ball’s Stopgap 1200 smoothing compound can also be applied over steel subfloors and carries the wheel mark logo and UK conformity mark. It has the additional feature of being suitable for use over old adhesive residues, and when used in such applications, there is no need to prime beforehand.
The latest advancements in technology have enabled F. Ball to create a fast-track, water-mix smoothing compound that can be applied over old adhesive residues which has recently been approved for use in marine environments: Stopgap 1500.
Marine-certified heavy-duty smoothing compounds are available for areas that will be subject to high foot traffic and heavy loads prior.
Adhesive selection
When choosing an adhesive for marine flooring installations, factors to consider include likely exposure to water, extreme temperatures or temperature fluctuations.
Included in F. Ball’s marine range, Styccobond F81 epoxy adhesive can be used where floorcoverings will be exposed to surface water because the adhesive is waterproof.
For areas where vinyl floorcoverings will be exposed to extreme temperatures or temperature fluctuations, contractors can use Styccobond F49 Hybrid PS, a temperature tolerant, pressure sensitive vinyl adhesive that creates a high-strength, water resistant bond to hold resilient floorcoverings in place across a wide range of temperature fluctuations, from as low as -20°C up to +60°C.
F. Ball’s recently launched Styccobond F58 PLUS is a fast-drying, fibre-reinforced, pressure sensitive adhesive that is also suitable for the installation of LVT floorcoverings in marine and offshore environments. Its fast-drying formulation enables LVT tiles and planks to be secured from just five minutes following application of the adhesive. It can also be used to install rubber floorcoverings, a popular choice on ships because they are durable, easy to maintain and often offer better grip when wet.
MED-certified adhesives for a wide range of textile floorcoverings, which also carry the UK conformity mark, are also available from F. Ball, including its Styccobond F3, a popular choice for bespoke carpet installations on board luxury cruise liners, as well as the company’s Styccobond F41 carpet tile tackifier.
Compatibility check
It is always advisable to check that an adhesive is suitable for use with a particular floorcovering. To do this, flooring contractors can see F. Ball’s Recommended Adhesives Guide (RAG®) or consult manufacturers instructions. Alternatively, F. Ball’s technical service department are on hand Monday to Friday, 8.30am – 5.00pm, to answer your questions about F. Ball products and how to use them.