This website uses cookies so that we can provide you with the best user experience possible. Cookie information is stored in your browser and performs functions such as recognising you when you return to our website and helping our team to understand which sections of the website you find most interesting and useful.
About Us
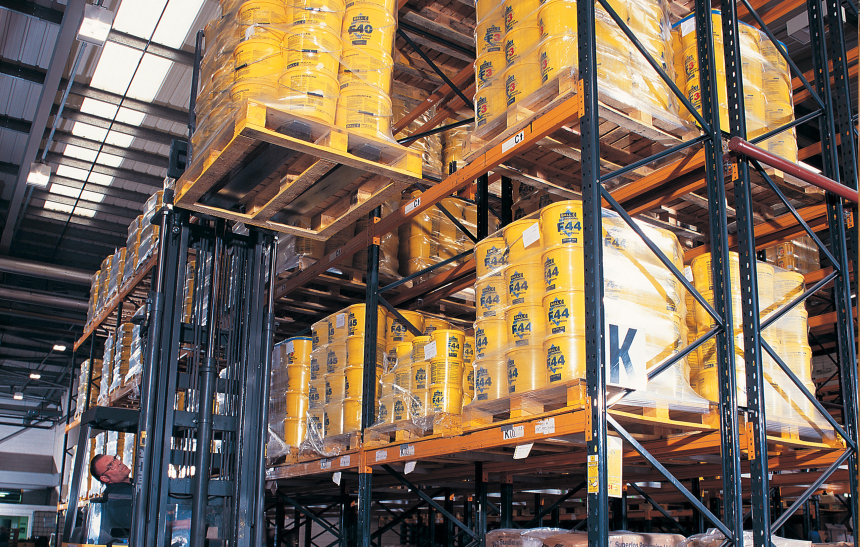
The F. Ball Philosophy
F. Ball is dedicated to creating the next generation of products to help flooring professionals meet ever higher customer expectations, with increasing ease and efficiency, underpinned by industry-leading customer support.
Watch our video for an overview of the company, including history, products, manufacturing processes, approaches to research and development, testing and quality control, as well as industry-leading customer service.