Sticky situations
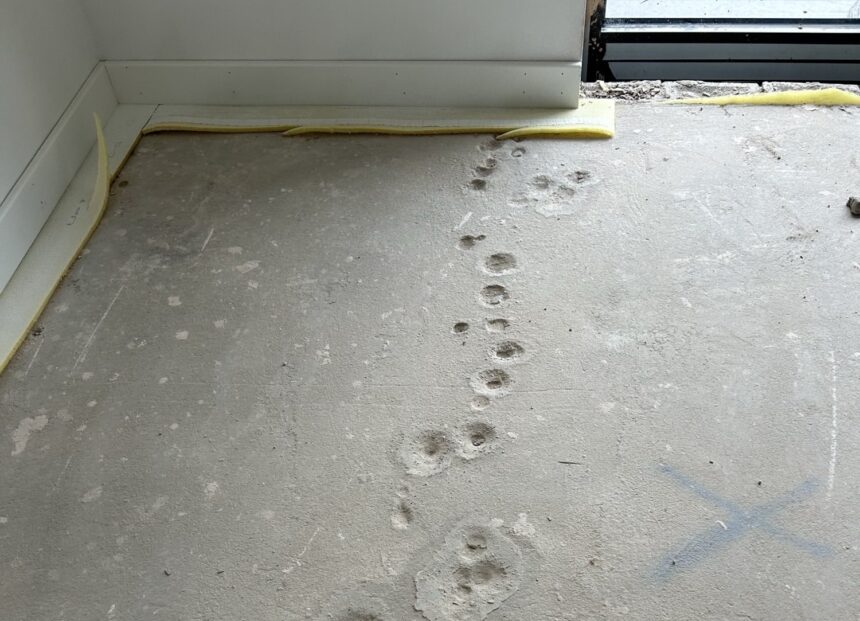
Gary Kenworthy advises on additional steps that you might need to undertake where subfloors are in a poor condition.
The first step in any flooring installation should be to make sure that a subfloor is suitably sound, smooth, dry and free of contaminants to avoid floor failure. This is more or less straightforward depending on the condition of the subfloor – it can involve more processes if a screed is damaged.
This was the case when we were asked to advise on subfloor preparation ahead of installing sheet vinyl in kitchens and bathrooms of 49 flats, each with an area of approximately 500m2, over three floors of a newly built retirement development. The subfloor was a 75mm thick sand/cement screed, installed around four months previously.
The situation
Although most of the building was made watertight around two months ago, a few areas were still open to the elements. The screed was cracked in places, with some surface divots. It was also contaminated with paint and plaster residues throughout.
We noted patches of surface water in several areas, and a moisture test also indicated that subfloor Relative Humidity (RH) levels ranged from 78% to 96%. BS 8203, Code of practice for installation of resilient floor coverings, stipulates that subfloor moisture levels must be lower than 75% RH before proceeding with the installation of resilient floorcoverings or a moisture management solution is deployed. Otherwise, there is a chance that excess subfloor moisture could attack adhesives and floorcoverings, causing them to debond and, ultimately, leading to total floor failure.
Our solution
Based on the above observations, we recommended the following course of action to ensure a successful flooring installation.
It would first be necessary to make sure the building is fully weather-tight and allow the screed to dry until there was no visible moisture.
The contractors should then mechanically remove any contamination and rake out cracks and divots before vacuuming to remove any dust and debris. They could then use Stopgap 460 Exterior Repair mortar to fill the cracks and divots, providing they were found to be static and not propagating. A fast-setting repair mortar that can be used to fill non-structural cracks from 3-30mm, Stopgap 460 Exterior is specifically designed for use in damp conditions, including external environments. This meant that it could be applied to the damp subfloor prior to the application of a waterproof surface membrane.
Moisture management
We recommended a single coat of Stopgap F77 waterproof surface membrane to create a barrier between excess subfloor moisture and subsequently applied subfloor preparation products, adhesives and floorcoverings. It should be applied using a 1.5mm x 5mm v-notched trowel, before rolling with a pre-coated roller to achieve a continuous pinhole-free finish.
Once the waterproof surface membrane had cured, it was recommended that the surface was primed using F. Ball’s Styccobond P141 primer. It is specially designed to promote the application characteristics of smoothing compounds when applied to non-absorbent surfaces, including waterproof surface membranes.
When the primer was dry, contractors could apply a minimum 3mm thickness of Stopgap 1200 Pro smoothing compound and allow it to dry to create a perfectly smooth base for floorcoverings.
Adhesive recommendation
Finally, we advised that LVTs were installed according to the manufacturer’s instructions using an adhesive listed as compatible in our Recommended Adhesives Guide (RAG®).
Pressure sensitive adhesives, such as F. Ball’s Stycobond F46, are usually recommended for the installation of LVTs because they form an instant grab upon contact, stopping tiles or planks moving about as contractors work, and their extended open time reduces the risk of late placement. A pressure sensitive adhesive with moisture tolerant properties, such as Styccobond F49 Hybrid PS, might be used in the bathrooms where floorcoverings could be exposed to damp conditions.
In this case, the application of a waterproof surface membrane avoided having to wait for the screed to dry naturally to a level below the threshold where floorcoverings could be installed without the risk of floor failure, which could have taken weeks or months.
Gary Kenworthy is F. Ball technical representative for the North West.
F. Ball’s regional technical representatives provide advice to flooring contractors on how to get the most out of F. Ball products, including conducting site visits and producing case-specific reports advising on the best course of action for particular flooring projects. Find out who your technical representative is here.