Tech Advice: Working over flexible subfloors
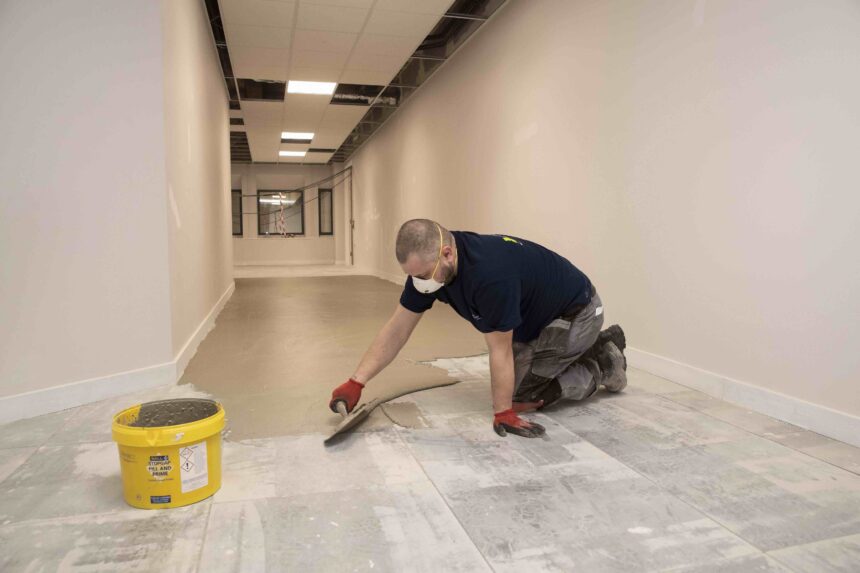
Guidance on preparing metal and wood subfloors ahead of the installation of floorcoverings, including choosing the right smoothing compound.
Preformed subfloors, such as metal and plywood, can move slightly when subject to normal foot traffic. For this reason, specialist smoothing compounds, which are better able to accommodate these movements, have been developed for creating a suitable base for the receipt of floorcoverings when working over these kinds of subfloor.
The choice of floorcovering and the condition of the in situ subfloor will determine the requirement for a smoothing compound or a finishing compound, and contractors need to follow best practice when preparing the subfloor beforehand.
Prior preparation
The first step in any flooring installation should be to ensure that the subfloor is suitably sound and smooth before commencing work.
In the case of preformed subfloors, this means ensuring that plywood overlays are securely screw-fixed to substrates at regular intervals in accordance with the British Standards. Joints should be effectively supported to prevent any vertical displacement when loaded. Where flooring installations are part of a refurbishment, old adhesive residues should also be removed, or boards replaced.
Filling in the gaps – finishing compound
Where subfloors are made up of panels, in the case of raised access floors, for example, it will be necessary to fill the gaps between them, as well as holes caused by screws used to affix wood panels to the substrate so that they do not transfer to imperfections in the appearance of the finished installation.
Floor finishing compounds, such as F. Ball’s Stopgap Micro Rapid, can be applied to a seamless micro feathered edge to fill indentations formed by screws used to secure plywood and hardboard sheets. Stopgap Micro Rapid will also fill in gaps and take out any minor discrepancies where boards meet. The ultra-smooth, flexible, rapid-drying floor finishing compound creates a flawless subfloor finish, where a smoothing compound is not required. It is walk-on hard and ready to receive new floorcoverings from just 20 minutes after application, and priming is not required prior to use, making it ideal for use when working to tight time constraints and deadlines.
Priming – prior to applying a smoothing compound
Traditionally, it is almost always essential to prime subfloors at this stage. Priming promotes the application characteristics of subsequently applied smoothing compounds and adhesives, particularly when used over absorbent subfloors, such as plywood, as well as preventing smoothing compounds from drying too rapidly, resulting in a reduced working time. It also helps to prevent pin-holing, caused by tiny bubbles resulting from the slow escape of air from the subfloor, which burst on reaching the surface, leaving small pinholes or craters as the smoothing compound dries.
For when working over metal raised access panels, cement-based primers, including F. Ball’s Stopgap Fill and Prime, are available that fill the gaps between flooring panels whilst priming the subfloor, saving valuable time. They have a thixotropic consistency, meaning that they flow freely when stirred but set to a gel-like consistency on standing, enabling the joints to remain filled. They are also suitable for use over well-bonded, waterproof adhesive residues, prior to the application of the recommended smoothing compound.
Fibre-filled smoothing compounds
Where the base has been suitably primed and gaps between raised access panels have been filled, contractors should proceed to apply a fibre-filled smoothing compound, such as F. Ball’s Stopgap 700, to create a perfectly smooth base for floorcoverings.
The product is reinforced with tiny fibres that maintain the integrity of the smoothing compound, preventing cracks from forming as a result of minor subfloor movement caused by foot traffic or temperature fluctuations. It is suitable for application over plywood and steel subfloors, including raised access panels, as well as concrete and sand/cement screeds.
Stopgap 700 is also fast setting. It is walk on hard just 60 minutes after application and allows floorcoverings to be installed in as little as three hours, while maintaining a working time of 20–30 minutes, making it ideal for projects where time is tight and reducing the time that areas are out of use. Its protein-free formulation makes it suitable for use in biologically sensitive areas, such as laboratories and hospitals, and it is approved for marine use.
Final thoughts
The development of high-performance floor finishing compounds has equipped installers with an ideal solution when time or floor height are critical. Installers need to make the right choice, between using a fibre-filled smoothing compound or a finishing compound that will remove minor surface defects and create a perfectly smooth surface for floorcoverings, without the need to prime, when working over plywood and hardboard.
Following the steps outlined here will ensure the integrity and appearance of a flooring installation for many years to come, avoiding costly remedial work and saving valuable time and money.