The knowledge: Dealing with damp
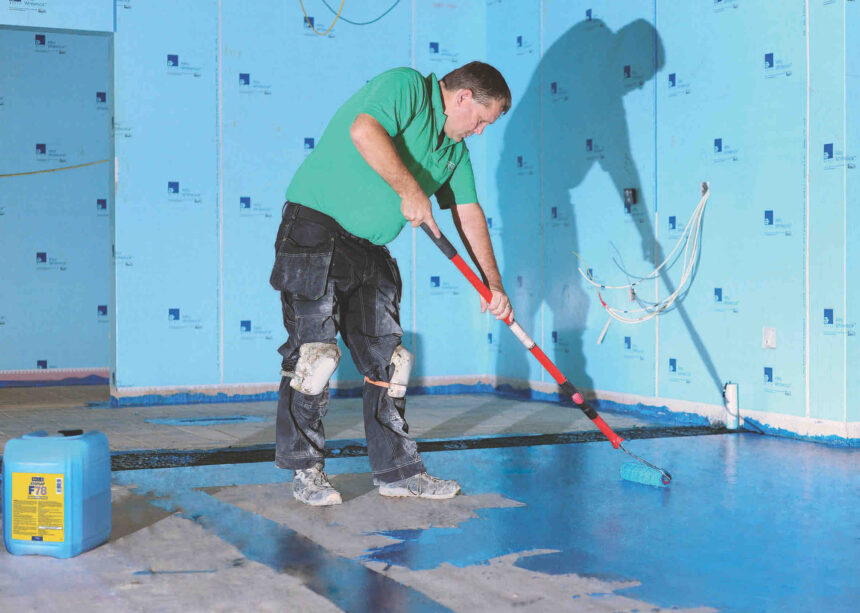
In this series, we tell you what you need to know to ensure flooring installations live up to high customer expectations.
For this first issue, we start at the bottom, advising on the importance of identifying and dealing with the leading cause of floor failure: excess subfloor moisture.
Unchecked subfloor moisture, whether residual construction moisture, the result of concrete not completely drying, or rising damp, from the ground beneath, can attack flooring adhesives and floorcoverings. This may cause wood to warp, damaging textile floorcoverings by promoting mould and bacterial growth and result in resilient floorcoverings, such as vinyl and Luxury Vinyl Tiles (LVTs), blistering and lifting. Not only can this ruin the finished appearance of a flooring installation, it can result in complete floor failure and present a health hazard.
F. Ball’s technical service department frequently receives enquiries about rectifying flooring installations where floorcoverings have begun to lift as a result of unmanaged excess subfloor moisture, and our regional technical representatives often attend site visits where this is the case.
Testing
For these reasons, in addition to ensuring a subfloor is suitably sound, smooth and free of any contaminants, it is important to take time to determine subfloor moisture levels as part of the subfloor preparation process and, where necessary, deploy an appropriate moisture management solution.
The only way of measuring subfloor relative humidity levels with accuracy, and the method advocated by British Standards, is using a calibrated digital hygrometer.
Where Relative Humidity (RH) levels are above 75% where resilient or carpet floorcoverings will be installed, or 65% for wood flooring installations, a liquid waterproof surface membrane will normally be required to suppress excess subfloor moisture and prevent damage to flooring.
Solutions
F. Ball has two timesaving options for when a moisture management solution is needed. Stopgap F77 waterproof surface membrane is a two-part, epoxy resin system, which is applied in a single coat. It fully cures in as little as three hours and will isolate residual construction moisture or rising damp where relative humidity values are up to 98%.
For an even quicker way to create a barrier against residual construction moisture where RH values are up to 95%, there is Stopgap F78, a one-component system, which is applied in two coats, requiring 15–20 minutes curing time for the first and a further 30 minutes for the second.
Next steps
After checking for subfloor moisture and deploying a moisture management solution where required, the rest of the subfloor preparation process can proceed. This will usually include the application of a smoothing compound to create a perfectly smooth base for the receipt of the floorcoverings, remembering to prime beforehand if necessary.
We’ll deal with subsequent subfloor preparation and installation processes in future issues.
F. Ball’s technical service department is on hand Monday to Friday, 8.30am – 5.00pm to answers your questions about subfloor preparation and floorcovering installation and can also arrange site visits to identify and advise on the best course of action for any flooring project.