This website uses cookies so that we can provide you with the best user experience possible. Cookie information is stored in your browser and performs functions such as recognising you when you return to our website and helping our team to understand which sections of the website you find most interesting and useful.
Technical Help & Advice
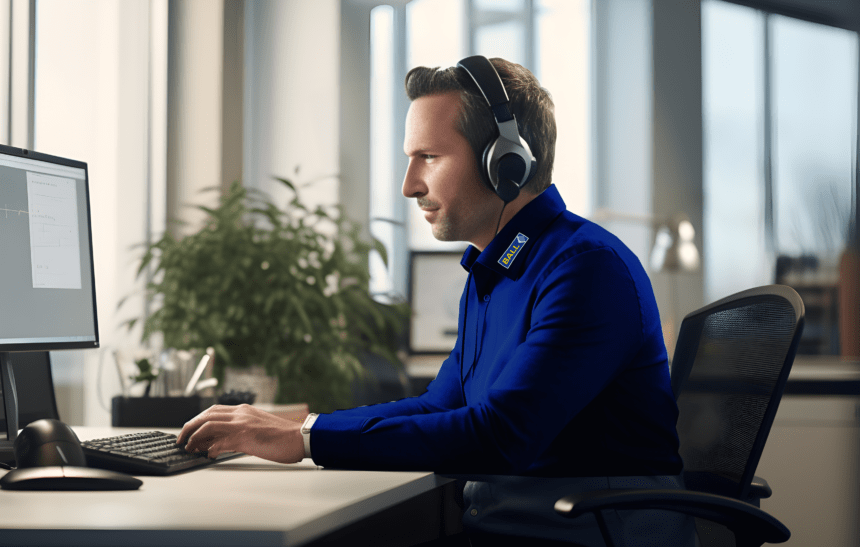
Our Experts
Our technical services team deal with around 11,000 enquiries a year across the UK and Ireland. We’re never too far away if you need more hands-on support. Our team are continually trained on the latest products, advice, safety and data to ensure they can answer all your questions.
How to Contact Us
During working hours (Monday-Friday 8.30am-5pm), you can reach us by phone on 01538 361633, or you can contact us via Live Chat (on the right hand side of the screen) or WhatsApp, and we’ll aim to get back to you in minutes.
Download our RAG® app
F. Ball’s Recommended Adhesives Guide (RAG®) has earned the trust of many contractors, becoming their most valuable asset for flooring adhesive solutions. Download our mobile app for iOS and Android to ensure your RAG is always up to date with the latest recommendations. This means you have access to our expert advice 24/7.
FAQs
No, the expansion joint should be taken up through the floor finish and a suitable expansion joint/cover fitted.
No, most smoothing compounds are polymer modified and have a controlled level of absorbency.
Adhesive manufacturers spend a great deal of time developing adhesives for installing specific floor coverings. It is essential that the correct amount of adhesive is applied, and the method of application is normally the ‘V’ notched trowel. If the notches are worn, the amount of adhesive applied is reduced, and the open time of the adhesive is also reduced. The combination of these two factors makes it more likely to have a flooring failure, and the financial consequences can be horrendous.
In general, the answer is yes, although there are some instances where priming is not necessary, as explained below.
Priming of absorbent floors reduces the absorbency. This will increase the open time of the adhesive, thus reducing the possibility of late placement. In addition, it will reduce the possibility of pinholing that can occur when smoothing compound is applied.
Priming of non-absorbent subfloors with a suitable primer, such as undiluted Stopgap P131, will act as an adhesive promoter for the smoothing compound.
Priming is not generally necessary when applying reactive adhesives such as polyurethane or epoxy systems.
If boards are cement faced, secured with CTA or screws – then prime first with Stopgap P131 neat. Locate the mesh using minimal tape and encapsulate with either Stopgap 700, Stopgap 1200 or Stopgap 1600. Two layers will probably be needed to stop mesh from floating and 3mm clearance from the top of the wires should be obtained.
Ensure the ceramic tiles are sound and well bonded over a permanently dry base. They must be clean and grout lines should be lightly raked out. Apply Stopgap P141 gritted primer then the appropriate Stopgap floor smoothing compound.
We would recommend that the chipboard is overlaid with a minimum of 6mm thick flooring grade plywood to stabilise the chipboard. The plywood must meet BS8203 (Annex A) and should then be primed with dilute Stopgap P131 prior to installing the vinyl using the recommended adhesive.
All floors need to be carefully examined for moisture. The visual inspection of a subfloor is inadequate as the surface may appear dry, but moisture may still be present.
In the first instance, an indicative test using a radio frequency moisture meter offers a quick and easy method of testing moisture levels, providing an instant reading to indicate whether moisture is present. If no moisture is present, the flooring installation can proceed as planned. However, if a radio frequency meter indicates that a subfloor contains moisture, further investigation is required to enable the identification of an appropriate treatment.
To accurately assess the level of moisture in the subfloor, measurements should be made at a number of points across a floor over a period of between 4 and 24 hours. According to the British Codes of Practice (Sections BS 8203, BS 5325 and BS 8201 addressing the installation of resilient, textile and timber floorcoverings, respectively), it is recommended that a non-invasive method is used for dampness testing, such as a calibrated digital hygrometer.
Temporarily sealed to the floor to isolate the device from the surrounding air, a digital hygrometer provides a direct reading of the Relative Humdity (RH) of a small volume of air in equilibrium with the subfloor. Where RH levels are measured below 75%, the surface is considered sufficiently dry to receive the floor covering, and the installation can proceed without further treatment. If the RH level exceeds 75%, further treatment is required.
As wood floors are particularly sensitive to moisture, F. Ball recommends a maximum RH level of 65%. However, due to the specialist nature of wood flooring, contractors should seek advice from the wood flooring manufacturer before proceeding.
Products such as Stopgap 1200 and Stopgap 1500 can be used over firm and well bonded bitumen adhesive residue. However, thermoplastic and vinyl asbestos tiles were very often laid on ground floor subfloors that did not incorporate a damp-proof membrane. The adhesive was unaffected by moisture, and the tiles allowed the passage of moisture vapour. Modern formulations of vinyl tiles are considerably more sensitive to moisture vapour. It is, therefore, essential that the presence of a damp-proof membrane is confirmed.
If not, then it may be necessary to include Stopgap F77 in the build up of the floor. In this instance a DPM sandwich would typically be adopted: Stopgap 1200 or Stopgap 1500 to isolate the bitumen/Stopgap F77 to impede damp rising through the floor/Stopgap 1200 or Stopgap 1500 to smooth and receive the floorcovering.
As the installation of a damp-proof membrane in new buildings only became mandatory in 1965, the ground floor levels of buildings which were constructed before this date should be subjected to a moisture measurement test. Moreover, if a building has been compromised by a leak at some point, the floor should be tested, even if it is above ground floor level.
New buildings will incorporate a damp-proof membrane, but they still remain susceptible to moisture as the drying time of a new sand/cement screed is estimated to be 1mm per day up to a thickness of 50mm. A 150mm thick concrete subfloor can take up to a year to dry out naturally. Therefore, to ensure that a concrete subfloor is sufficiently dry to receive a floorcovering, all new build projects should be tested for moisture.
Prior to installing a resilient or textile floorcovering, it is essential to ensure that the subfloor incorporates an effective damp-proof membrane, in accordance with British Standards BS 8203 and BS 5325, respectively.
Moisture testing is performed by measuring the Relative Humidity (RH) level within a subfloor. Where the relative humidity (RH) is above 75%, the installation should not proceed as the excess moisture in the floor can result in blistering of the floorcovering or complete failure of the flooring installation. This may result in expensive and lengthy remedial work, including the possibility of an expensive ‘rip out’, to allow the subfloor to dry naturally or apply an appropriate waterproof surface treatment.
By testing the subfloor for moisture at the outset, this can be avoided, and moisture can be effectively dealt with prior to the installation of floorcoverings.
If P5 chipboard or OSB3 which is mechanically fixed and glued at T&G, the Fill and Prime followed by Stopgap 1200 or Stopgap 700 are possible.
All our adhesives are approved for use with underfloor heating – but the underfloor heating must be switched off 48hrs before, during and after installation of a new floorcovering, with a temperature when in operation not exceeding 27°C at the bond line.
Get In Touch With Our Experts
Use the form below to ask a question to one of our teams, including sales, technical support and training queries.