Choosing the Right Smoothing Compound
The application of a suitable floor smoothing compound or smoothing underlayment helps to ensure a perfectly smooth base for the receipt of new floorcoverings, ensuring subfloor imperfections do not transfer to the finished installation. While general-purpose smoothing compounds are ideal for many situations, there are also scenarios when it is advantageous, or even highly recommended, to use a smoothing compound with specialist features.
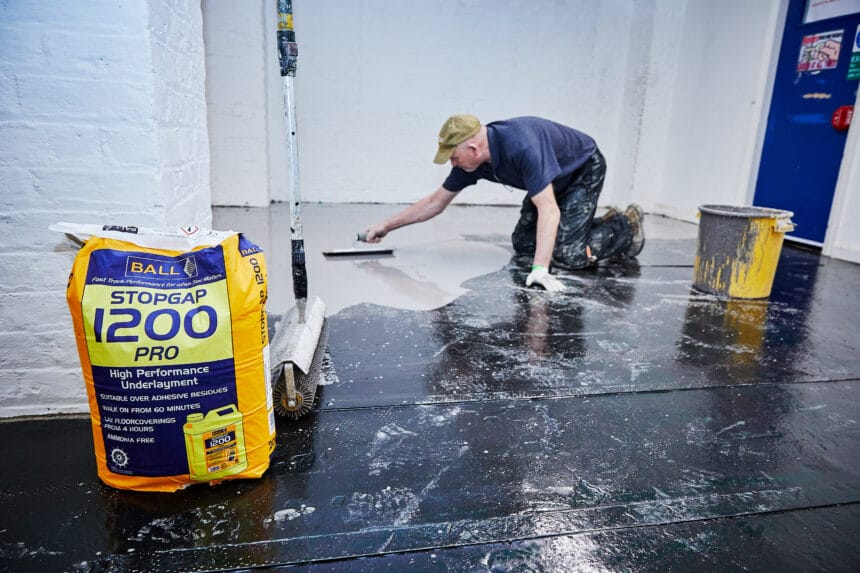
These products have been developed to provide a long-lasting, professional flooring finish, as well as to optimise the installation process in particular situations, such as when working to tight timescales or installing floorcoverings over certain subfloor types.
Fast-track applications
Many recent innovations in smoothing compounds have helped to speed up the subfloor preparation process, supporting contractors under pressure to meet strict deadlines, without compromising on finished results.
The fastest-drying products are walk-on hard from just 30 minutes after application and ready to receive floorcoverings in as little as 45 minutes later. Many are suitable for use over a wide range of subfloor types, including sand/cement and concrete screeds, as well as application over waterproof surface membranes.
Adhesive residues
Another development that has sped up subfloor preparation is the formulation of smoothing compounds that can be applied directly over old adhesive residues, eliminating the need to spend valuable time mechanically removing them. In most cases, there is no need to apply a primer when opting for this type of smoothing compound, saving further time and expense. Market-leading versions, such as Stopgap 1200, allow floorcoverings to be installed from just four hours.
Traditionally these products have only been available in bag and bottle form. However, recent advancements in cement technology have enabled the development of water-mix alternatives, providing another choice for contractors. As a water-mix smoothing compound, no bottle is required, reducing the plastic waste produced by the flooring industry.
Plywood or steel
The application of a smoothing compound that is designed to accommodate slight movements or flexing in the subfloor is recommended when working over subfloors of plywood or steel.
These products are reinforced with tiny fibres that maintain the integrity of the smoothing compound when subject to minor subfloor movement as a result of normal foot traffic or temperature fluctuations.
Heavy-duty applications
When it comes to preparing floors that will be subject to heavy loads or high levels of foot traffic, a heavy-duty smoothing compound should be selected for its high compressive strength, which will ensure that installations can withstand this kind of treatment for years to come.
Such smoothing compounds are a popular choice for preparing subfloors in retail settings, schools and hospitals. The excellent self-levelling properties of select heavy-duty smoothing compounds also help ensure the optimal base for designer flooring.
Other smoothing compounds
Calcium sulphate screeds have become an increasingly common choice of subfloor, especially in new-build properties and where underfloor heating is incorporated within the subfloor. Manufacturers of calcium sulphate screeds advise that a calcium sulphate-based smoothing compound is applied when dealing with this type of subfloor as both components shrink at the same rate during the drying process, limiting the amount of stress at the bond interface.
Initial preparations
Before a smoothing compound is applied, the subfloor must be checked to ensure that it is suitably sound, smooth and dry enough for the receipt of subfloor preparation products and floorcoverings. This should include the removal of any old adhesive residues, unless a specialist smoothing compound is used that can be applied directly over the top. There are also situations where additional preparations, such as the application of a repair compound, will be required to achieve a perfectly smooth base; for example, where sand/cement screeds are mechanically damaged.
A subfloor moisture test should be undertaken as part of any flooring installation. Where relative humidity (RH) levels within the subfloor are above 75% (65% if installing bonded wood floorcoverings), the application of a waterproof surface membrane will be required to prevent excess subfloor moisture attacking adhesives and floorcoverings, potentially leading to floor failure. The application of a primer is also recommended in almost all circumstances prior to installing a smoothing compound.
After these steps have been undertaken, the application of an appropriate smoothing compound is the final stage in the subfloor preparation process before new floorcoverings can be installed.